The electrolyzer enigma: How solving it could enable the energy transition
They have been around for a hundred years, but still, we barely understand electrolyzers. Significantly though, these devices can be used to produce green hydrogen, therefore playing an essential role in the energy transition. That’s more than enough reason to unravel the secrets of the electrolyzer and to engineer one that is efficient, affordable, and modular so that it can be used on a large-scale. TU/e is doing exactly this, within the so-called Dutch Electrolyzer consortium, together with partners and companies. In six questions we take you through the enigma of anodes, bubbles, and electrolytes.
1. What can you do with an electrolyzer?
Without consciously knowing it, chances are you’ve already built an electrolyzer yourself. It is a typical experiment in high school in which you put two pins connected to a battery into a glass of water. Then, as you might remember, little gas bubbles formed on both ends of the pins.
These gas bubbles, which are hydrogen and oxygen to be precise, are the products of this electrolysis process in which electricity is used to split water molecules. In essence, an electrolyzer does just that on a much larger scale, where this process can be used to produce tanks full of hydrogen.
Producing hydrogen is what it’s all about. According to many, hydrogen can be a game changer in the transition to a CO2-neutral energy supply. It can be used in many different ways.
First of all, as an energy carrier, hydrogen is an attractive gas for large-scale and long-term storage of electricity generated from sun and wind technologies (and all thanks to electrolysis of course). Storage of electricity in hydrogen can help in dealing with potential fluctuations in electricity supply and demand. Next to that, the existing gas network can be used to transport hydrogen. Hydrogen can also be used in fuel cells to provide electricity, for example in means of transport.
Finally, hydrogen is a key building block in the production of chemicals, together with CO, which is obtained by CO2 electrolysis. In a number of chemical production processes, hydrogen can contribute to alternative CO2-free methods, including ones that currently emit a lot of CO2 such as the production of steel or fertilizer.
By using hydrogen generated from renewable energy sources, the chemical industry, which is traditionally associated with pollution and waste, can become significantly “greener.”
And what’s one of the greenest ways to produce hydrogen? Yes, you guessed it—using an electrolyzer.
2. What is the problem with today’s electrolyzers?
The electrolyzer has been around for over a hundred years and in essence they still look the same. Or, as TU/e researcher Thijs de Groot puts it: “Beautiful technology, but it’s like we’re still driving around in a Ford Model T from the 1900s.”
De Groot, who is jokingly referred to as mister electrolyzer by his colleagues at TU/e, has been working on electrolysis all of his life, both industrially and in academic research. He still combines his work at the university with a position in industry within Nobian, the largest player in industrial electrolysis in the Netherlands.
“Relatively little R&D” has been done on the most commonly used electrolyzer, the so-called alkaline electrolyzer, which has been applied on large scale since 1930, according to De Groot. “They’re still pretty heavy, expensive devices that don’t produce so much hydrogen.”
So, to play a significant role in the energy transition, electrolyzers need an urgent upgrade. “To be able to upscale the production of hydrogen with electrolyzers, they need to become cheaper, more efficient and more flexible,” says De Groot.
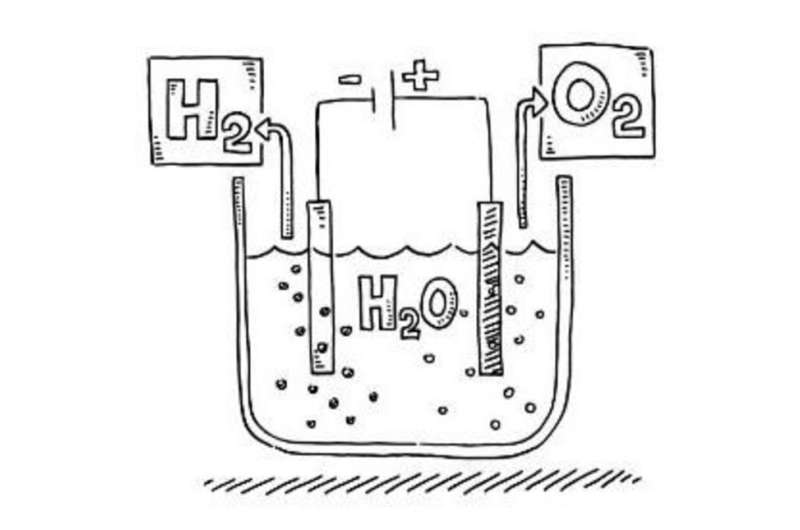
This is the main goal of the Dutch Electrolyzer consortium, a collaboration of TU/e’s energy institute EIRES with DIFFER (Dutch Institute for Fundamental Energy Research) and VDL Group and set up thanks to a grant from the province of Noord Brabant.
By improving the technology of electrolysis on the one hand, and at the same time gaining insight into how it can fit into the market on the other, the various parties want to arrive at a production of a new type of electrolyzer that allows you to produce hydrogen on both a small and large scale.
“A large-scale solution will always consist of several identical units,” says Marius Ponten, Director of Corporate Innovation at VDL. An important question is therefore what the optimum module is for scaling up. Ponten: “To be very specific, is it cheaper to build a gigawatt plant from 500 kilowatt units or from 20 megawatt units?”
How do we engineer the ideal electrolyzer?
Well, that’s not so easy. Despite the fact that they have been around for over a hundred years, we still don’t fully understand electrolyzers. “If you look at the properties of the various components, you expect a much better performance than currently is the case,” says De Groot. “And we don’t have a clear reason why that’s so disappointing.”
So how can we solve this puzzle? The approach at TU/e is to go back the basics. Several sizes and types of electrolyzers can be found on the campus. To expose and learn to understand all aspects of an electrolyzer—each ‘puzzle piece’ – in detail. “With 3D printed electrolyzers, for example, we try out different shapes,” says De Groot. “What happens then? And do we understand that?”
A special feature of the Dutch Electrolyzer project is that it is multidisciplinary: from physics to mechanical engineering, and from electrical engineering to chemistry. Unique areas of expertise in which TU/e leads the way come together here, such as the manufacturing of scalable electrochemical reactors, thin film synthesis for the very precise control over material properties and knowledge on electrocatalysis and electrode engineering.
De Groot: “We are slowly getting a sharper picture of the puzzle.”
4. Could it be bubbles that affect the efficiency?
Bubbles? Indeed, perhaps ironically the gas bubbles produced are themselves a suspect when it comes to the disappointing power output from electrolyzers.
“It is known that if there are bubbles in the electrolyte the current cannot pass through it as easily,” says researcher Bert Vreman, who works at Nobian and at the TU/e, in the Power & Flow group of Niels Deen in the department of Mechanical Engineering. He does not rule out the possibility that you can gain significant increase of efficiency or capacity (current density) with some minor improvements.
But how do you send those bubbles somewhere else? There are several possibilities, according to Vreman. “An obvious one is to pump the electrolyte solution around faster, but you can also think about a different geometry for the reactor, a different shape of electrodes, a different material from which bubbles are released faster. But it’s not clear how much these things matter.”
What complicates matters significantly is that you can see so little of the bubble-production process in a working electrolyzer. “Everything is white, like a wild river. So filming it doesn’t give much information. That’s why Vreman, Deen and colleagues are now looking first at simplified situations, for which they perform detailed computer simulations.
In this way, they can study how one electrolytic bubble grows, and from this a lot can already be learnt. “You have to deal with two-phase flow (liquid and gas), surface tension, electrochemical reaction, concentration gradients, heat transport, and electric current around the bubble,” Vreman lists. “All those mini-processes we want to fundamentally understand.”
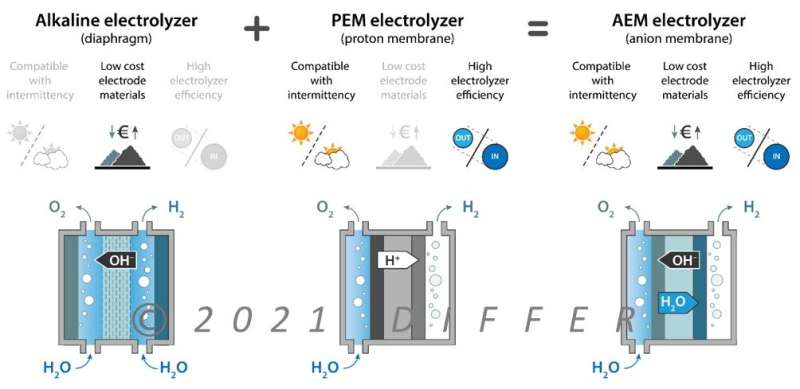
5. Can we perhaps do something about the electrodes?
Electrodes are also an obvious candidate for a closer look. Often scarce precious metals and compounds are used for the electrodes, such as platinum and iridium oxide. Iridium is one of the rarest materials on earth, which naturally drives up the cost of an electrolyzer considerably.
That’s why the teams of Adriana Creatore (Applied Physics department) and Marta Costa Figueiredo (Chemical Engineering & Chemistry department) are looking at alternatives. “We are looking for more readily available and cost-effective materials, without compromising on efficiency and long-term stability,” explains Creatore. To this end, they are also working closely with Mihalis Tsampas’ group at DIFFER.
Specifically, they are focusing on the reaction at the anode, during which oxygen is created, a process known in technical terms as the oxygen reduction reaction (OER). Creatore: “This reaction starts very slowly and the needed electrocatalyst requires long-term operational stability, be made out of earth-abundant materials and be low in cost to be produced at large scale.”
The team of Creatore currently adopts atomic layer deposition (ALD) to achieve control over the composition of the electrocatalysts down to the size of atoms. Currently, they are investigating compounds based on elements such as cobalt and phosphorus, or nickel.
“We are currently benchmarking these catalysts to currently used electrocatalysts using fundamental and well-defined set ups and conditions,” says Costa Figueiredo. “Our plan is to use several spectroscopic techniques to explore reaction mechanism and changes on the electrode due to electrolysis operation.”
6. What makes the Dutch electrolyzer project so special?
Ask those involved and you will get the same answer from everyone: the combination of parties involved and expertise, both in the field of fundamental research and industrial practice, creates the ideal basis for developing and commercializing electrolyzer technology.
It is worth noting that there are other horses to bet on, besides the most well-known alkaline electrolyzer variant that TU/e is particularly focused on. In recent years, other promising electrolyzer technologies have emerged. Mihalis Tsampas and his research group at the energy institute DIFFER are focusing on these.
These include, for example, the use of polymer or ceramic ion-conducting membranes instead of a liquid electrolyte in so-called polymer electrolyte membrane electrolysis (PEM). “This brings the significant advantage of small intra-electrode distance compared to conventional alkaline electrolysis,” says Tsampas.
“This could lead to reduced resistance and faster system response.” A step further even is the so-called AEM electrolyzer, an emerging technology which shows great promise since it combines the advantages of PEM and alkaline electrolysis (see image).
On the other hand, solid oxide electrolysis, involves working at high temperatures and ceramic metal oxides perform the role of electrolyte. “Due to their temperature window, such reactors offer unique opportunities not only for water electrolysis but also for the production of sustainable chemicals and fuels,” says Tsampas.
The fact that there is a direct link between research and industry means that potential electrolyzer advancements will find their way more quickly into final products. Ponten of VDL: “The focus is initially on ‘quick wins’ and improving already mature techniques, and for the longer term we are assessing alternative, more innovative processes to develop further.”
With all the relevant expertise together, a technological roadmap for the electrolyzer is within reach. And that can’t happen fast enough. European demand for hydrogen is expected to be 20 times greater than current global production capacity by 2030.
Citation:
The electrolyzer enigma: How solving it could enable the energy transition (2021, September 16)
retrieved 17 September 2021
from https://techxplore.com/news/2021-09-electrolyzer-enigma-enable-energy-transition.html
This document is subject to copyright. Apart from any fair dealing for the purpose of private study or research, no
part may be reproduced without the written permission. The content is provided for information purposes only.
For all the latest Technology News Click Here
For the latest news and updates, follow us on Google News.